But new research from consulting firm Fails Management Institute (FMI) indicates that the design-build (DB) delivery method, where an owner contracts with a single entity to perform both design and construction, is quickly gaining traction in the industry. According to the June 2018 “Design-Build Utilization” report, DB methods will represent nearly half, or 44%, of construction put-in-place (CPiP) spending across many market segments by 2021.
FMI predicted that collective DB CPiP spending in these segments will increase 18% between 2018 and 2021, swelling from $274 billion to $324 billion in value. Manufacturing, educational and highway/street segments are expected to comprise the top three market shares of 16%, 15% and 14% by 2021, respectively, followed by commercial with a 13% share.
No longer the “alternative”
Design-build and other alternative delivery methods like construction manager at risk (CMAR) and construction manager/general contractor (CMGC) have become more attractive options to owners wanting to tighten up project budgets and/or timelines, according to the study. Alternative methods were “indicated to provide the best avenue to achieve the originally identified cost,” the report found.
While 82% of owner respondents said they’ve used or plan to use DBB in the next five years, 58% of owners said they’ve used or plan to use DB.
Given the popularity of DBB, just over half of owners surveyed said usage would stay about the same over the next five years while 32% predicted a decrease and only 15% predicted an increase. Meanwhile, 29% of owners said DB adoption would stay the same while 67% predicted increased utilization.
One reason that DB methods have gained momentum, according to the report, is the passage of state legislation that facilitates the use of alternative project delivery methods. Last year, for example, Virginia legislators expanded design-build authority to all local governments, the New York governor’s budget added new state entities to the list of those authorized to use design-build and the Washington state legislature recommended design-build for construction of a bridge. Legislation in 38 states that enables use of public-private partnerships also plays a role in boosting DB utilization, the report found.
Get construction news like this in your inbox daily. Subscribe to Construction Dive:
“The use of alternative delivery methods in general is growing and will continue to do so, particularly design-build, as projects become more complex and need to be delivered in an expedited fashion,” said FMI consultant Paul Trombitas in a webinar hosted by the Design-Build Institute of America (DBIA).
Advantages, obstacles to adoption
Design-build methods promote a “culture of collaboration” that’s not always present in traditional contracting arrangements, Trombitas said. From the start of a project, designers and contractors in DB projects share decision-making and pitch unified project recommendations to the owner for meeting the owner’s schedule and budget, according to DBIA.
Seventy-six percent of owner respondents to FMI’s survey rated their experience with DB as “very good” or “excellent.” They cited increased opportunities to innovate and the ability to fast-track a project as the top two benefits of DB.
In contrast, “the almost contentious relationship that design-bid-build or low-bid pricing creates doesn’t allow for the innovation, early collaboration and identification of effective solutions to deliver projects,” according to Trombitas.
Plus, traditional project delivery methods can pit the designer and contractor against each other when project obstacles arise or changes are required, DBIA says, sometimes leading to litigation and project delays. In a collaborative DB relationship, however, change orders by the owner are less likely.
While DB contracting offers potential time and cost savings, making the switch to this alternative model sometimes requires owners to make a cultural shift. Owners often have to adapt their contract management practices and adjust to a smaller role in the design process. Another potential disadvantage for owners is less competition because of the smaller number of companies that can pull together an effective DB team.
However, FMI expects DB use to pick up as owners gain more exposure to the advantages of the approach. “A continued emphasis toward educating owners and project stakeholders on the process and benefits associated with design-build will facilitate continued adoption and greater utilization,” the report found.
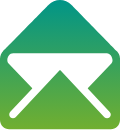
STAY UP-TO-DATE!
Subscribe to receive our newsletters with insights and tips from industry experts.
RECENT ARTICLES
Commercial Construction Lead Generation Platforms and Tools
Commercial construction lead generation platforms and tools. Discover early-stage data, public bidding sites, networking opportunities, and CRM integration.
The Ultimate Subcontractor’s Guide to Winning More Commercial Construction Bids
Struggling to find relevant construction bids? This guide reveals the challenges subcontractors face and how specialized platforms like Construct-A-Lead provide a competitive edge.
Expert Insights: Why Verified Data Matters in Construction Lead Generation
Understand why accurate, verified construction lead data is crucial. Learn how verified project details save valuable time, reduce frustrations, and increase bidding success.